Recently, the quality inspection and the quality department have frequently responded to the ceramic foam filter sprayed dead hole. The quality department has several assessment items for the workshop, and the production internally finds the cause and analyzes the root of the problem.
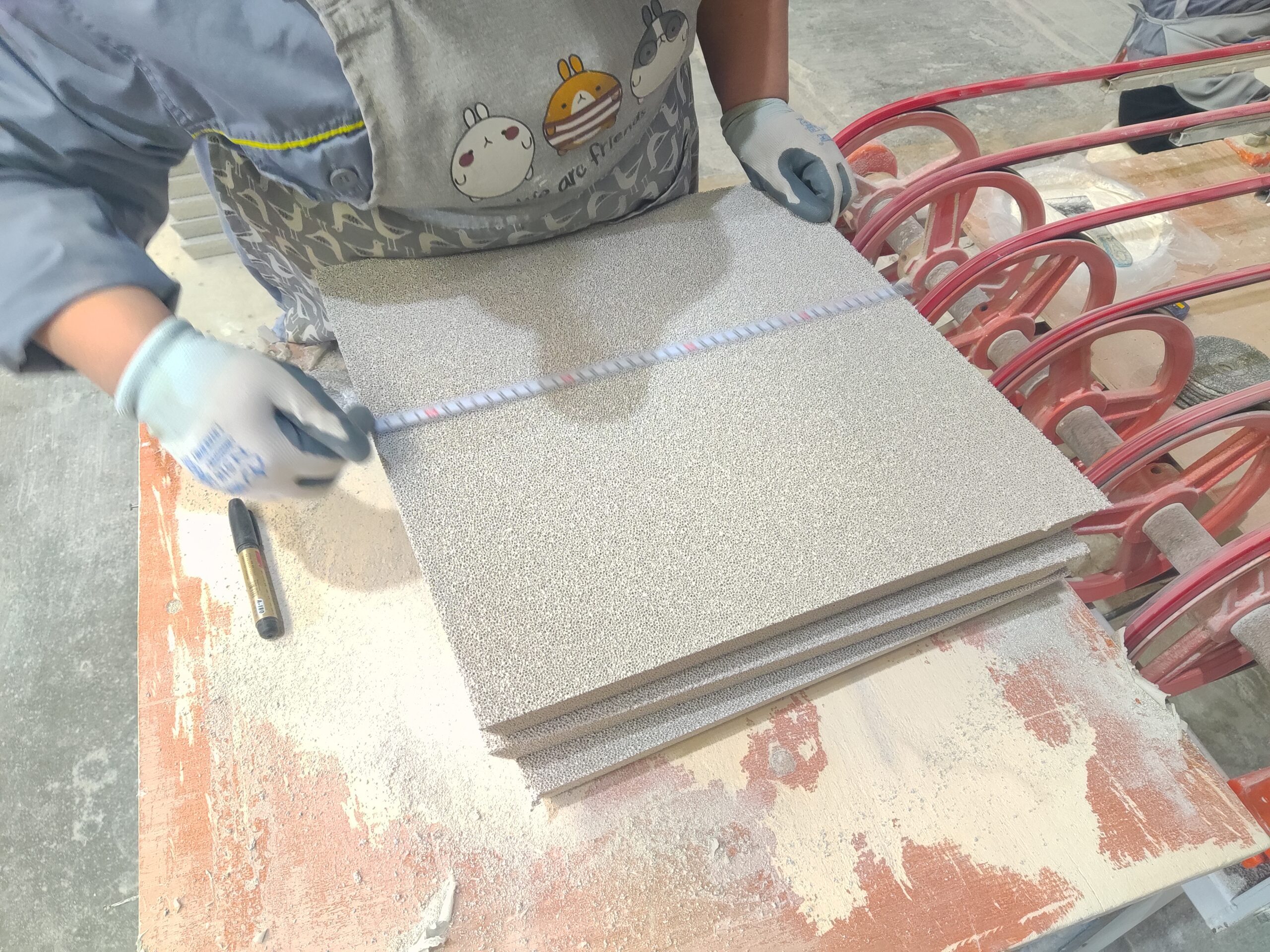
ceramic foam filter
ceramic foam filter sprayed dead hole–Problems in the spraying process:
- Spray A on the large surface of the porous ceramic filter has always been sprayed and atomized, but the atomization effect of sprayed B is not good. The filter plate checks the amount of slag, pore size, and the appearance quality of the plate surface to check the quality of the large surface, so the effect of spray A There must be no problems; at this stage, the spraying A spraying is uneven, sometimes good and sometimes bad, sometimes large and sometimes small, and the frequency of dropping points is high. There are scrapped products every day, and the pass rate of spraying quality random inspection is low.
Reason analysis: 1) The internal design of the sprayed grout A is different from that of the sprayed grout B. The sprayed grout A feed tank has been damaged, and there are many gaps in the corrosion of the feed tank, which is the direct cause of the dropping point; 2) Spraying A has always been less effective than spraying B. The possible reason is that the position and structure of the spraying head of spreading A are different from that of spraying B; 3) The effect of replacing the old motor of streaming A is not good. The shotcrete flow pipe has too many openings, is too long, and the opening is too large. The self-made pipe is not standard and does not match the spray wheel. The overall position of the spray wheel does not match the original design. The direct cause of spraying is big and small, drop point, and uneven; 4) The spraying wheel is old and worn. After cleaning, each wheel can not be installed in the original fixed position, and the spacing of the wheel is different. , the spraying effect is significantly reduced;
Suggested rectification measures: 1) The fastest solution at this stage is to exchange the positions of spraying A and B, let spraying B spray the large surface, and spray A to spray the small surface; 2) replace the new spraying A wheel Flow pipes that match the standard; 3) Weld the spraying A material receiving tank to repair the leaking material, and compare the size and angle of the receiving tank with the spraying B after repairing;
- Infrared transmission often stops suddenly. If you want to restore it, you can only cut off the power of the spray line as a whole, and then restart the system, so that the transmission can continue to run. In this case, workers need to readjust the spray volume every time. There are 2-4 pieces of uneven spraying and more or less spraying, which has a great impact on the stability of product quality and continuous production.
Cause analysis: The control parts displayed on the control screen panel of the spray line do not match the actual ones. The operation starts the spray A, and the operation on the screen may start to spray B or start the turning machine. This kind of disruption of the wiring of the operating system may cause It will cause system interference, resulting in poor PRC operation and system software crashes.
Suggested rectification measures: 1) Restore the operation control system that the equipment manufacturer just started to debug and run, and match it with the control screen panel to prevent human error; 2) If it still happens after restoration, check whether there is a fault in the system operation.