Ceramic foam filter and process for preparing same
Description
BACKGROUND OF THE INVENTION
ADTECH FILTER is drawn to an improved ceramic foam filter for use in filtering molten metal, especially Aluminum base alloys, and a process for preparing same. More particularly, ADTECH FILTER relates to a ceramic foam filter having improved properties especially with respect to the filtration of Aluminum base alloys to the provision of rapid priming with respect thereto, and not being reactive therein.
The production materials for these filters comprise primarily a phosphate bonded refractory material, having certain other additions, which has been fired to a temperature of about 2000° F. in order to mature the bond. While this type of refractory is suitable for use in the aluminum industry and easily withstands most aluminum alloys which are typically cast at about 1300° F., it is unsuitable for many other potential applications due to low strength and poor chemical resistance and poor high temperature stability.
Naturally, it would be highly desirable to develop a material which maintains the favorable properties of the ceramic foam material heretofore known, namely, high porosity, low pressure drop, high geometric surface area and tortuous flow path, but which overcomes the foregoing difficulties of strength, chemical durability and temperature resistance. In addition, it is highly desirable to develop a material which could be relatively simply produced and used in a number of applications especially high temperature applications, such as for the filtration of ferrous metals.
ADTECH describes an improved ceramic foam filter and a process for preparing same particularly useful for high temperature applications such as ferrous or steel filtration based on the use of an aqueous slurry of a thixotropic ceramic composition including a gelled alumina hydrate binder. It has been found that for certain applications, specialized running and gating systems are needed to insured priming of this filter, although said filter does represent a significant improvement.
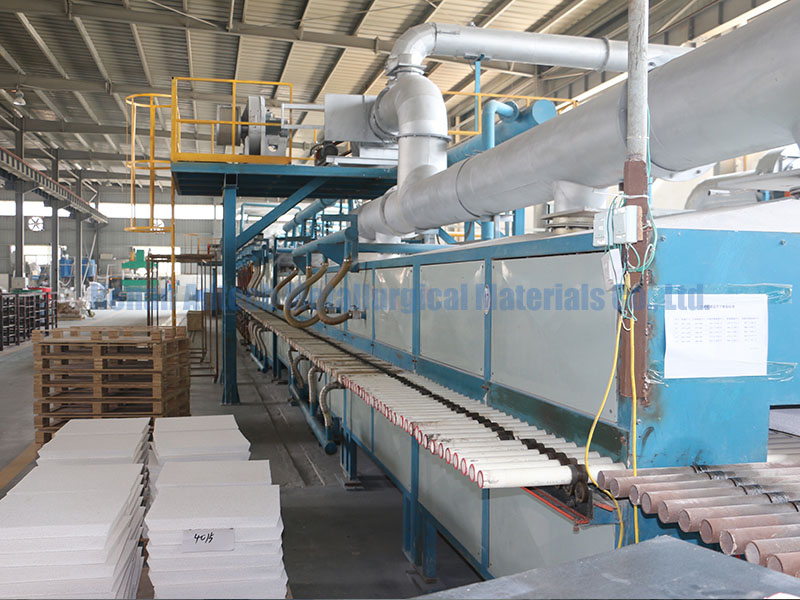
Ceramic foam filter and process for preparing same
ADTECH provides an improved Ceramic foam filter and process for preparing same.
ADTECH provides an improved ceramic foam filter and process as aforesaid which is inexpensive and easy to perform and which results in a filter having desirable and indeed improved properties.
ADTECH provides an improved filter and process as aforesaid which overcomes the shortcomings of phosphate binders and which provides a filter which is readily primed and has improved thermal properties.
SUMMARY OF Ceramic Foam Filter
ADTECH provides an improved ceramic foam filter and process for preparing same which is characterized by excellent physical properties especially high thermal conductivity, and by rapid priming with respect to iron and iron base alloys, and which avoids the shortcomings of phosphate binders especially thermal/chemical instability resulting in phosphorous pick-up in the molten metal.
The improved ceramic foam filter of ADTECH is prepared from a ceramic slurry containing silicon carbide and a colloidal silica binder which comprises an open cell structure with a plurality of interconnected voids surrounded by a web of said ceramic, said filter having a solids content of at least 50% silicon carbide and at least 3% silica, preferably 3 to 15% silica. Other ceramic materials may readily be added to the slurry, such as alumina.
In addition, ADTECH resides in a process for preparing a ceramic foam filter for filtering molten metal which comprises: providing a reticulated, organic polymer foam; impregnating said foam with an aqueous slurry of a thixotropic ceramic composition including silicon carbide with a colloidal silica binder, said composition having a solids content of at least 50% silicon carbide and at least 3% silica, preferably 3 to 15% silica; drying and heating said impregnated polymer foam to remove the organic components therefrom, and firing at an elevated temperature to produce said ceramic foam filter.
The process and filter of ADTECH obtains significant advantages in the art especially with respect to the filtration of iron and iron base alloys. The colloidal silica has been found to have a wetting effect on the final product with respect to iron and iron base alloys and therefore obtains rapid priming in the filtration of molten iron an