ceramic filter plate: Filter-PAl filter plate uses organic foam with a three-dimensional network structure and connected pores as the carrier, and invades it into the thixotropic Al20s material slurry, and adopts the automatic extrusion process of square correction center distance to make the slurry The material is evenly coated on the foam body skeleton of the carrier, and it is baked at a high temperature of 1180°C after drying and curing. Installed in the filter box for aluminum alloy liquid impurity filtration, meeting the production of high value-added, high-tech performance aluminum alloy precision casting for the aviation industry.
If the pore size of the ceramic filter plate is large, it will affect the purity of aluminum liquid filtration. If the pore size is too small, the service life of the ceramic foam filter will be reduced, and the replacement frequency and use cost of the customer will be increased. Therefore, in order to provide customers with more refined ceramic filter plate products, each department of Ivans strictly controls the quality of raw materials and operating procedures. To enable customers to use better quality, more cost-effective products.
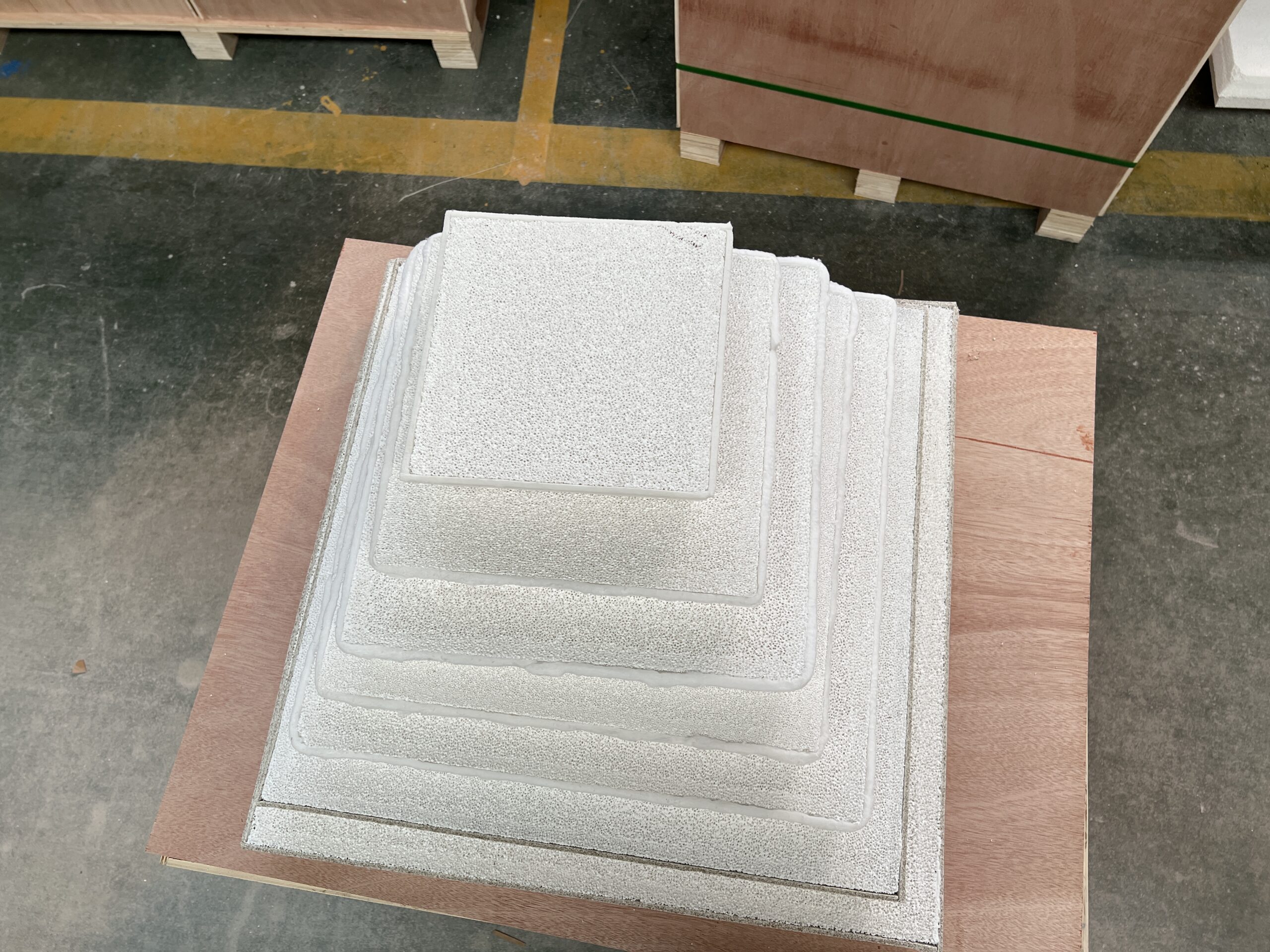
ceramic filter plate
①After the customer orders, the salesman provides the porous ceramic filter
sample to the quality officer, and the quality officer measures the exact pore size.
Since different companies have different definitions of pore size and mesh, this ensures that the mesh number of filter plates produced by Ivans is consistent with customer requirements.
②The quality officer will provide the foam sample block corresponding to the pore size to the purchaser. After the purchaser compares the price and quality of the supplier, the high-quality supplier will be determined and the sample block will be sent for production.
vesicle-like block
③After the foam body arrives, the quality personnel conducts a random inspection to observe whether the surface of the foam body is smooth, whether there are gaps, blocked bags, mixed packaging, etc. Make sure that the bubbles entering the production are qualified products. If the above situation occurs, return the raw materials to the supplier and re-produce qualified foam.
gap
Packet
④ The quality officer uses a microscope computer to further measure the pore size of the sampled bubbles. Only when the pore size is within the qualified range can the foam body be transferred to the workshop.
Microscope Computer Aperture Measurement
⑤In the process of cutting the foam body, individual cutting edges of the foam body do not meet the qualified requirements. At this time, equipment maintenance and design personnel will fine-tune, adjust and overhaul the precision of the cutting machine. To ensure the final production of qualified products.
Equipment maintenance and adjustment of cutting machine precision
Ivans people are constantly working hard to adhere to customer-centered and excellence!